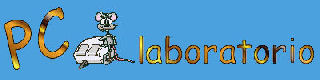
REGOLAZIONE DELLE VENTOLE DI RAFFREDDAMENTO
Ecco un altro argomento "base", uno dei più gettonati sia a livello PC (modding e non solo!) sia a livello di raffreddamento di apparecchiature elettroniche in genere. E' un argomento come detto molto "gettonato" e al riguardo basta una ricerca con un motore qualsiasi per trovare decine di siti e forum che si dedicano alla questione, con idee e progetti di ogni tipo. L'idea che mi spinge a mia volta a dedicarmi all'argomento è proprio questa: le ventole di raffreddamento (soprattutto se molto "importanti" come nel caso di CPU e simili) DEVONO poter svolgere al meglio la loro funzione. Anche se si tratta di componenti "secondari" e semplici, occorre considerare che ne esistono di svariati tipi e soprattutto ne esistono di più o meno robuste. La loro alimentazione "teorica" è quasi sempre 12 Vcc (OVVIO che in questa sede si tratterà di questo tipo di ventola, anche se ne esistono di alimentate direttamente in alternata a 220V), mentre i consumi in genere sono fra i 100 e i 300 mA. TROPPO SPESSO mi è capitato di imbattermi in progetti o consigli che NON sono di certo il massimo in termini di durata o di sicurezza per la ventola, e di conseguenza per l'apparato che deve raffreddare (!). Vorrei perciò dire la mia idea, che deriva da diverse sperimentazioni e che ho potuto ampiamente mettere in pratica ottenendo sempre buoni risultati in tutta sicurezza.
Innanzitutto (a parere mio ovviamente), salvo alcuni casi particolari, NON vale la pena sottoporre a regolazione manuale ventole che possono essere regolate automaticamente (quindi a seconda delle necessità) dal sistema. Mi riferisco in particolare alla ventola delle moderne CPU. La mainboard ha già un sistema integrato di regolazione ottimale per questa ventola in relazione alla temperatura raggiunta dalla CPU stessa. Impiegare una regolazione manuale in questo caso porta alla necessità (ASSOLUTA!) di tenere sempre sotto controllo la temperatura (via software o hardware) per poter intervenire prontamente in caso di necessità. Se ci si distrae o non si regola il flusso di aria in modo ottimale si corre il rischio di avere come minimo un sistema instabile a causa del surriscaldamento del processore e conseguenti (micro o macro) interventi delle protezioni! La regolazione manuale di questa ventola va secondo il mio parere riservata a situazioni SPERIMENTALI E TEMPORANEE. Nell'uso normale del PC cercare di ridurre la rumorosità a discapito della comodità di uso e della stabilità non mi sembra una buona idea.
Diverso può essere il caso delle ventole di raffreddamento della GPU (Scheda grafica). Qui in effetti può essere utile poter regolare il flusso d'aria in base all'uso: basso per l'uso normale, alto quando si sfrutta al massimo la potenza video (videogiochi, montaggio video). Anche in questo caso però occorre prestare attenzione alla temperatura raggiunta per evitare danneggiamenti.
Dove invece secondo me si può intervenire molto più liberamente (oltre che con efficacia e con buoni risultati sulla rumorosità generale!) è sulle ventole del case e su quelle (eventuali) di raffreddamento degli hard disks. Qui le temperature sono decisamente molto meno critiche e variano in modo abbastanza lento. Sono inoltre più basse e vicine a quella ambiente, tanto che si può giocare sulla velocità della ventola anche in relazione alla temperatura della stanza (più lente in inverno e più veloci in estate, salvo riscaldamento e/o condizionamento del locale!). Un piccolo software di controllo (ad es. DTemp) è più che sufficente per tenere sotto controllo la temperatura dell'HD, sempre che non si disponga già di un apposito software in genere in dotazione alla scheda madre (tipico il PC Probe delle Asus, che oltre alle temperature di CPU e mainboard fornisce tutti i dati sulle alimentazioni).
Passiamo alla REGOLAZIONE. Il discorso in sè è semplice: la velocità di rotazione della ventola è più o meno proporzionale alla tensione di alimentazione. Occorre tuttavia tener presente che al di sotto di una data tensione (dipende anche da tipo e marca della ventola, ossia dalle sue caratteristiche) la ventola si ferma. Ma soprattutto i problemi si possono avere in avvio! Sotto un dato voltaggio la ventola NON parte, e soprattutto il motorino (anche se parte) subisce uno stress, tanto che se la ventola non è particolarmente robusta o di marca rischia di rompersi! In linea di massima dalla mia esperienza e dai dati raccolti in giro per il web, direi che l'ideale è NON scendere al di sotto della metà della tensione di alimentazione o poco meno. Per ventole da 12 Vcc sarebbe opportuno rimanere sempre al di sopra dei 5-6 Vcc di alimentazione. In queste condizioni la rumorosità è già molto bassa rispetto al pieno regime e si ha sempre lo spunto per la partenza senza troppa "fatica". Ammesso che ci sia una proporzionalità diretta (non è esattamente così), una ventola che al massimo gira a 3500 rpm quando è alimentata a 5 V scende a 1400-1450 rpm, il che non è poco (provate e soprattutto ascoltate: il rumore sarà molto basso!).
Quanto ai METODI di riduzione del voltaggio se ne vedono di ogni!!! Alcuni mi sento di SCONSIGLIARVELI senza dubbi. Evitate di ricorrere a diodi in serie e a simili "brutture"!! Le resistenze semplicemente messe in serie alla ventola possono teoricamente dare il risultato voluto (ovviamente non vi è possibilità di regolazione), ma non lo trovo un sistema degno di attenzione, se non in "emergenza". Intanto va determinato il valore della resistenza (vale il calcolo spiegato nel dimensionamento delle resistenze per i LED!). In questo caso però l'assorbimento di corrente è più alto (100-300 mA per ogni ventola), il che comporta la necessità di usare resistenze di potenza adeguata. Inoltre la potenza dissipata viene ovviamente trasformata in calore, quindi aspettatevi che la vostra resistenza scaldi parecchio! Tanto per fare un esempio, per una sola ventolina che assorbe 200 mA e per farla funzionare a 5 Vcc partendo dai 12 Vcc la resistenza (da circa 35 ohm) dissiperà circa 1.4 Watts. Dovrete prenderne una da almeno 5 W nominali e vi assicuro che comunque scalderà parecchio.
ATTENZIONE: (qui di certo molti mi daranno torto, ma mi sento di dirvi ciò che penso!) a volte al posto della resistenza fissa vengono utilizzati dei potenziometri, ossia delle resistenze variabili, con l'intento di rendere il tutto regolabile. Bene, NON FATELO O FATELO A RAGION VEDUTA ! Come principio è corretto e potrebbe anche funzionare, ma i "normali" potenziometri in vendita (negozi di elettronica), ammesso di trovare valori resistivi abbastanza bassi, sono quasi sempre del tipo "a strato di carbone" (un cursore che scorre su uno strato di grafite). Bene, questi dispositivi NON SONO IN GRADO di dissipare la potenza richiesta!!! Se non bruciano subito ben presto la regolazione non è più lineare e prima o poi si bruciano (e il peggio è che se brucia il potenziometro la ventola si ferma!) .
Se proprio volete utilizzare un potenziometro per questo scopo ne dovete trovare uno che sia del tipo detto "a filo" e che dissipi almeno 5W. Non sono facili da reperire e sono decisamente più costosi dei normali. In questo caso il cursore scorre su un filo metallico (che è la resistenza) variando il valore in ohm. In ogni caso vale quanto detto per le resistenze fisse: con l'uso il potenziometro tenderà a scaldare (tanto di più quanto più lentamente starà girando la ventola).
Alcuni Autori impiegano schemi di variatori della tensione basati su integrati regolatori (tipicamente il LM 317), che forniscono in uscita una tensione stabilizzata e regolabile. Il sistema può essere impiegato con successo ed è valido, ma ricordate che dovrete dimensionare i componenti in modo che la tensione di uscita parta da 5-6 V!!!! E NON da zero o quasi (come spesso si vede!), altrimenti per metà rotazione del potenziometro la ventola non solo non parte, ma rischia di rovinarsi!
SOLUZIONI PROPOSTE
1) LA VIA PIU' SEMPLICE
Spesso (ad esempio per le ventole du un hard disk) la regolazione continua è persino "sprecata": bastano tre modalità. Ventola spenta, ventola a bassa velocità (e rumorosità), ventola al massimo (per ambienti caldi, in estate, o per uso pesante del PC). E' la soluzione che ho impiegato personalmente per l'hard disk di uno dei miei PC ed è molto comoda, visto che per la bassa velocità si dispone già della tensione di uscita a 5 Vcc dell'alimentatore del computer! La massima è ovviamente a 12 Vcc. In pratica tutto quello che vi occorre è un deviatore a zero centrale!! Eventualmente un deviatore doppio se come me volete associare l'accensione di un LED di diverso colore a seconda delle due velocità.
In pratica quando il deviatore è nella posizione centrale (ha tre posizioni in tutto) la ventola e i LED sono spenti. Da un lato la ventola (ed eventualmente il LED corrispondente) viene alimentata alla tensione minore, mentre se la levetta è dal lato opposto si avrà la massima velocità (12 Vcc).
E' un circuito così semplice che non richiederebbe schema. Ad ogni modo qui di seguito trovate le indicazioni per i collegamenti... potete aiutarvi con un tester se avete dubbi. Ricordate che nei connettori di alimentazione dei PC il/i fili neri sono la massa (il negativo), il filo rosso è il +5 Vcc e il giallo è il +12 Vcc. Vediamo di "semplificare" con un disegnino (scusate, ma non è il mio forte a mano!).

IMPORTANTE: in questo modo la ventola NON viene alimentata a 5 e 12 Vcc, bensì a 7 e 12 Vcc. Infatti uno dei capi della ventola è fisso a +12, mentre l'altro può essere collegato a +5 Vcc (e quindi la ventola riceve 12 - 5 = 7 Vcc) oppure a 0 (e quindi 12 - 0 = 12 Vcc), oppure (a deviatore in centro) è semplicemente non connesso (ventola spenta).
Ho preferito questo piccolo stratagemma alla semplice alimentazione a 5 Vcc perchè ho notato che alcune ventole già a questa tensione hanno difficoltà di avvio! Con 7 Vcc invece si ottiene sostanzialmente la stessa silenziosità ma in compenso l'avvio è sempre deciso e sicuro con tutti i modelli. Per curiosità i due LED sono alimentati a 5 Vcc come si vede dai collegamenti.
La realizzazione è stra-semplice: basta saldare i fili esattamente come sono disegnati! Il "pallino" nel punto dove due fili si intersecano significa che sono uniti. Alla fine vanno solo collegati (da un qualsiasi connettore PC) i fili nero, rosso e giallo rispettivamente ai punti indicati con "0V (negativo)", "+ 5V" e "+ 12V". Rispettare le polarità dei LED e della ventola (!). Potete alla fine racchiudere tutto in uno scatoletto a vostro piacere, eventualmente moltiplicando il circuitino per ogni ventola/gruppo di ventole che volete controllare. Qui sotto una immagine del mio prototipo (attualmente in funzione!) su cui ho montato dei LED da 10mm.

2) LA REGOLAZIONE DELLA TENSIONE
Questa è la soluzione per chi preferisce avere una regolazione più "fine" della velocità di rotazione della/delle ventole. Come detto in precedenza non è assolutamente auspicabile un circuito che alimenti la ventola con meno di circa 5-6 Vcc. La regolazione deve dunque avvenire nell'arco fra 5-6 e 12 Vcc. Come già detto, diversi circuiti possono svolgere egregiamente tale semplice lavoro, compresi quelli basati su regolatori di tensione. Personalmente (ma è una scelta!) credo sia molto più semplice utilizzare un semplice transistor di media potenza, come il BD 437 (o simili). Lo schema che ho provato e usato è il seguente:
Lo schema è di una semplicità estrema. Riporto anche la piedinatura del transistor per evitare errori. In pratica il potenziometro da 470 ohm regola la velocità, mentre il trimmer da 1000 ohm serve per la "taratura" del valore minimo di tensione. In pratica basta mettere un tester (o un voltmetro) al posto della ventola, alimentare il tutto a 12 Vcc, poi portare il potenziometro completamente al minimo della velocità (cursore tutto verso il trimmer, o comunque dal lato dove il tester misura la tensione più bassa). A questo punto regolando il trimmer si potrà regolare il valore in uscita fra 0 e circa 7,5 Vcc. Quella regolata sarà appunto la tensione MINIMA che giungerà alla ventola. Con il trimmer circa a metà corsa si otterranno 5.5-6 V. Regolare comunque per questa tensione. Infine verificare che ruotando il potenziometro la tensione salga da questo valore sino a 11.3-11.5 Vcc. Infatti a causa della giunzione del transistor si perderanno circa 0.7 V e quindi partendo da 12 V si potrà avere al massimo la tensione indicata. Questo comporta una MINIMA perdita di velocità massima della ventola (circa il 5%), che in genere non è neppure visibile ad occhio.
Il transistor (soprattutto per carichi oltre i 100 mA) sarebbe opportuno fosse dotato di un dissipatore di calore, anche minimo (sul tipo di quello visibile nelle prossime foto). Va infine notato che il circuito è valido sino ad assorbimenti di 2-3-400 mA (due-tre ventole). Aumentando di molto la corrente assorbita i valori di tensione in uscita tendono a scendere (si può compensare in parte riducendo via via il valore della resistenza da 47 ohm, sino ad eliminarla totalmente). Per la cronaca a circa 1A di assorbimento (sarebbero 6-10 ventole!) ed eliminando la resistenza da 47 ohm ho misurato un range di uscita di 5.5 - 11.0 Vcc partendo da 6.0 - 11.4 Vcc a vuoto. Ma direi che si tratta di un esperimento "limite". In genere è preferibile (in caso di molte ventole) replicare il circuitino: in questo modo ciascun gruppo di ventole può essere comandato singolarmente (es. quelle del case e quelle degli hard disks) e in più si evita l'eccessivo surriscaldamento del transistor. L'intero circuito ha un costo irrisorio (2-3 euro), quindi il doverlo replicare non costituisce problema da questo punto di vista.
Non necessitando (o non volendo) la possibilità di taratura della tensione minima si può sostituire il trimmer da 1000 ohm con una resistenza fissa da 470 o 560 ohm, ottenendo valori comunque accettabili di partenza. Io preferisco il trimmer anche perchè con alcune ventole più "sensibili" è possibile partire anche da 4 Vcc, mentre con le più "dure" si deve salire a 6 Vcc. In questo modo il circuito è sempre adattabile a tutti i modelli.
Qui sotto pubblico un paio di immagini del "prototipo" costruito su basetta millefori. Ciascuno può scegliere il metodo che più gli aggrada (millefori, montaggio in aria, circuito stampato...). Nel prototipo il potenziometro è stato sostituito da un secondo trimmer dotato di alberino plastico (lo si vede dal lato fili, quello opposto rispetto agli altri componenti). E' comodo perchè il tutto rimane unito in un solo pezzo facile da fissare ad un pannello. Il potenziometro è più "professional" e si regola meglio, ma dovrete collegarlo alla basetta con tre fili... bah, fate voi come preferite!
Unica cosa: notate che i cavi che portano la corrente più intensa sono di sezione maggiore rispetto agli altri (è importante soprattutto se prevedete più di un paio di ventole).
Bene, credo sia tutto. Mi scuso con chi di elettronica ne sa già, ma l'argomento "ventole" è molto gettonato e al tempo stesso si vedono in giro delle vere schifezze di progetti e/o consigli, che o non funzionano o rischiano di far bruciare la ventola nello spunto di partenza. Spero di essere stato utile almeno ai principianti o a chi si interessa soprattutto di PC e magari non di elettronica.
L'argomento potrebbe essere approfondito con molte varianti. Ad esempio non sarebbe molto più difficile dotare le ventole di termostato che le accenda o spenga a seconda della temperatura... Oppure per i "perfezionisti" si potrebbe pensare ad una regolazione molto più efficiente, controllando il motore della ventola in PWM... magari facendo uso di un microcontrollore appositamente programmato ed in grado di leggere anche le temperature e... perchè no, di mostrare il tutto su un display lcd! Anche se onestamente per un semplice controllo di una ventola del case non arriverei a tanto. Non sono un "modder" incallito... e i miei processori sono sufficentemente lenti da non richiedere particolari sistemi di raffreddamento! ;-)
Resto comunque a disposizione di chiunque abbia richieste e/o problemi.
BUON LAVORO!
_____________________________________________________________________________________________________
AGGIORNAMENTO
Su richiesta di alcuni visitatori interessati e per completezza ho deciso di aggiungere un piccolo sistema per chi desidera che la propria ventola (da PC ma anche di qualsiasi altra apparecchiatura, tipo alimentatori ecc.) sia controllata direttamente dalla temperatura dei componenti più critici. Come per gli altri circuiti ho voluto limitarmi a soluzione decisamente semplice e alla portata di chiunque, oltre che dal costo irrisorio (praticamente tutto può essere recuperato da schede elettroniche fuori uso!). Ho evitato comparatori e circuiti integrati. Solo un normalissimo transistor NPN (purchè di tipo Darlington) e pochi componenti passivi, oltre alla ventola.
Ecco lo schemino:

Semplicissimo, vero?! Eppure funzionale e veramente ok!
Il circuitino si presta a due differenti tipi di funzionamento a seconda della presenza o meno della resistenza R3. Così come è disegnato in pratica fa girare sempre la ventola al suo minimo, per aumentare il numero di giri sino al massimo solo quando la temperatura sale oltre un certo livello. Il valore dei componenti va un po' sperimentato. R3 (ho indicato 150 ohms ma non è detto che per la vostra ventola vada bene) è quella che determina la minima velocità di rotazione STABILE della ventola. In pratica deve avere un valore tale da permettere l'avvio da ferma e la rotazione costante al minimo numero di giri possibile. Dipende dalla ventola usata. Unica accortezza: usate una potenza di almeno DUE WATTS per questa resistenza. Se vedete che il motore della ventola tende a non partire con decisione non esitate a diminuire il valore sino ad ottenere appunto un avvio e una rotazione stabile.
R1 è una resistenza NTC, che quindi diminuisce la propria resistenza all'aumentare della temperatura. Ho scelto un valore di 10K solo perchè è facile trovarle su schede madri e pezzi in disuso. R2 è quella che regola la soglia di intervento (temperatura) del sistema. Con una NTC da 10K si può calcolare che fra 330 e 390 ohms (R2) si ha un intervento attorno ai 40 °C, che mi pare una temperatura accettabile. Abbassando il valore della R2 si alza la soglia e viceversa.
Il transistor è come detto un modello Darlington... vanno bene un po' tutti quelli di media potenza. Tanto per dare delle sigle i vari BDX 53, BDX 33, BD 675, BD 679 ..... Vanno tutti bene.
Il funzionamento è dunque questo: sino a circa 40-45 °C la ventola gira sempre, ma al minimo che avete fissato con la R3. Arrivati a quella temperatura il transistor inizia a condurre e quindi la ventola viene alimentata direttamente e non solo attraverso R3, quindi inizia ad aumentare la sua velocità sino al valore massimo. Al contrario raffreddandosi la NTC (che ovviamente va posta a contatto della parte che scalda, tipo alette di raffreddamento, dissipatori, ecc. magari fissata con del collante al silicone) la ventola gira sempre meno velocemente sino a stabilizzarsi tornando al suo minimo.
Il secondo modo di utilizzare il circuito è quello di tipo esclusivamente "ON-OFF". Basta eliminare la resistenza R3. In questo caso sino (e al di sotto) ai 40-45 °C la ventola rimarrà FERMA, mentre al superamento della temperatura critica si metterà in movimento sino alla sua massima velocità. Idem se la temperatura scende, ma al contrario di prima in questo modo sotto la temperatura di intervento la ventola si fermerà.
Ciascuno sceglierà il tipo di funzionamento in base alle caratteristiche dei propri progetti e a quanto preferito.
NOTA INTERESSANTE: se impiegherete questo sistema in un PC sarete normalmente vincolati dall'alimentazione (max. 12V). Se però necessitate di un sistema di raffreddamento molto efficace (si può fare per PC e per qualsiasi progetto) tenete presente che (a patto di subire una rumorosità maggiore) le ventoline 12V si possono spingere sino a 15-16Vcc senza danni, aumentando di molto la velocità e la portata di aria! ATTENZIONE: NON superate MAI i 16 Vcc pena la distruzione della ventola!! Per fare questo potete svincolare l'alimentazione della ventola/circuito dai +12V costruendo appositamente un piccolo alimentatore. Basta un trasformatore (2-300 mA), un ponte raddrizzatore, condensatore di livellamento, il tutto seguito da uno stabilizzatore di tensione tipo LM 317 e relativa circuiteria che lo porti a fare uscire appunto una tensione di 15-16 Vcc che userete sia per il circuito di controllo che per la ventola. In questo modo potrete sfruttare al massimo davvero il potere raffreddante della ventolina stessa, ripeto, a patto di accettarne la maggiore rumorosità.
Con questo per ora è proprio tutto. In caso di dubbi o chiarimenti sono sempre a disposizione.